Yearly Meet and Training Program of TSC Printers in Taiwan Exclusive
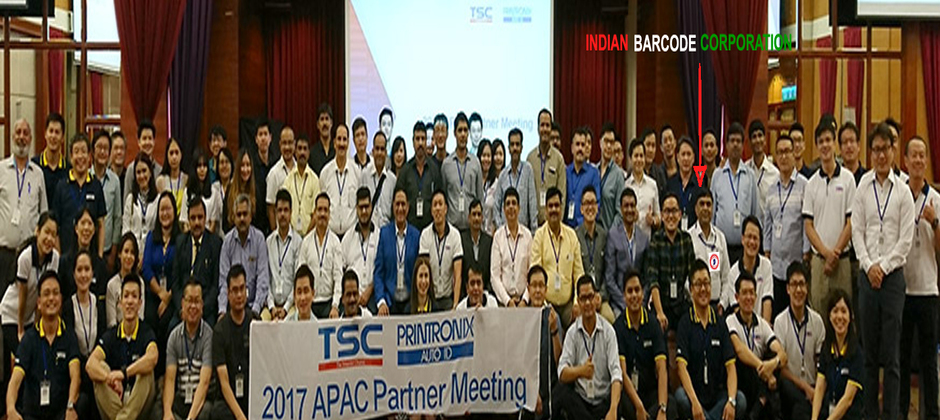
TSC Printers, the best Barcode printer manufacturer in the world now going to be more powerful and advanced, as a team with #MINDWARE. Our Leaders are attending the TSC Printers training in Taiwan and learning new strategies from the Barcode Printer Leaders so that #MINDWARE and TSC Printers will be able to climb every Mountain of Success together.
*Also here we have a tip for Inventory Management Best Practices for Your Organization:
1) Consider pursuing a demand-driven inventory management strategy.
Traditionally, many companies have taken a cost-driven approach to inventory management instead of one that is driven by demand. Cost-driven strategies, their essence, focus on getting inventory through a distribution network and reducing costs.
But switching to a demand-driven inventory management strategy can offer companies various benefits, as author William Brandel highlights in a Supply Chain Quarterly Article. Focusing on demand allows organizations to be more cost-effective, align their inventory with how (and when) their customers buy, have better forecasting accuracy, and reduce the possibility of overstocking inventory that goes to waste.
Making the switch isn’t easy and isn’t for everyone, but if your company decides to pursue this route, Brandel offers a few suggestions to achieve a demand-driven inventory management strategy. These include investing in forecasting software and/or inventory-optimization software, implementing supplier management strategies, and ensuring your systems have an application that contains an inventory-target calculation.
2) Optimize your inventory by using effective demand planning.
Ensuring ideal (or optimal) inventory levels can help your organization because holding inventory is more expensive than you might imagine, with some estimates of up to 60% of the cost of the item if it’s held for a year.
The goal is to align your inventory levels with what your business needs by focusing on demand planning. That way, you can reduce costs and not hold on to inventory that costs your organization significantly more than it’s worth.
3) Consistently review and redesign your inventory processes as needed.
There’s a common saying that rings true in any industry and application: “You don’t know what you don’t know.” This applies to inventory management. If you don’t review your inventory processes consistently, you won’t know if they aren’t working as well as they could.
And with how quickly the world is changing, from increased globalization to the implication of tariffs between companies like the U.S. and China, changes in compliance regulations, varying supply times, and the impact of natural disasters, it is possible that your current inventory processes may not be adequate for these changes anymore (or adaptable for future changes).
That’s where the benefit of reviewing your inventory processes comes into play. By inspecting them, you will see if they’re working effectively, and if you discover that changes are needed, you’ll have the information you require to redesign them to meet your current and future needs.
4) Use cycle counting to improve your inventory accuracy.
DC Velocity explains why using cycle counting instead of annual, manual inventory counts can improve a company’s inventory management. The biggest advantage, of course, is an accurate inventory. This improves your customer service, customer satisfaction, and speed to delivery.
There are a few ways to incorporate cycle counting into your warehouse or distribution center. First, you can use automated data collection tools like the barcode scanners and RFID readers offered by our friends at Datalogic and CipherLab. These tools – when integrated into a warehouse management software system – allow you to count and track your inventory in real-time. Second, you can do small batch counts instead of large product counts.
5) Consider using just-in-time (JIT) inventory management
Just-in-time (JIT) inventory management is defined as “a management strategy that aligns raw-material orders from suppliers directly with production schedules.” Since its adoption in the 1990s, this kind of management strategy has helped companies in several ways.
In a DC Velocity blog article by Dr. Keith A. Wade (American Public University), he explores the positive effects of JIT companywide. To begin with, there are no shortages in the materials a company needs so you can reduce your holding costs. But the price reductions don’t just stop there; you can also reduce prices across the board and reap savings that you can invest elsewhere (like in production or product development, for example).
Furthermore, by using JIT delivery, you can ensure a quick response to the demands of your customers and prospective customers.
Now, JIT isn’t for everyone. For companies involved in the energy industry, whether directly or indirectly, JIT isn’t always the best option. But overall, JIT offers numerous benefits that we can’t overlook.
Conclusion
- In summary, there are five inventory management best practices that can help your organization:
- Consider pursuing a demand-driven inventory management strategy.
- Optimize your inventory by using effective demand planning.
- Consistently review and redesign your inventory processes as needed.
- Use cycle counting to improve your inventory accuracy.
Consider using JIT inventory management.
Not all may apply to your company, but we hope that these give you some good starting points for boosting inventory management in your organization.